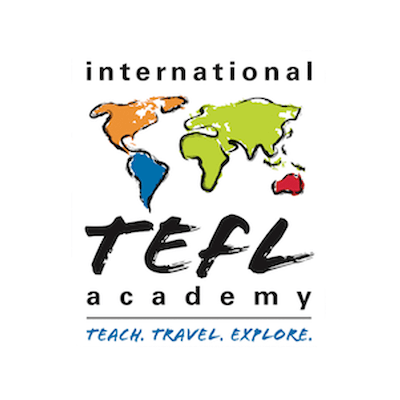
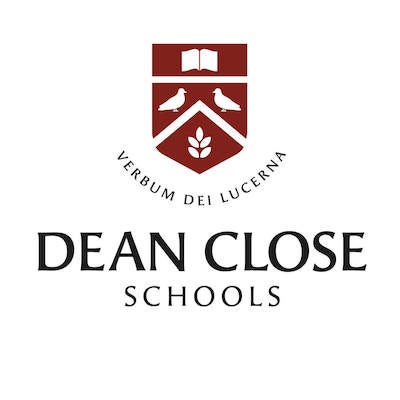
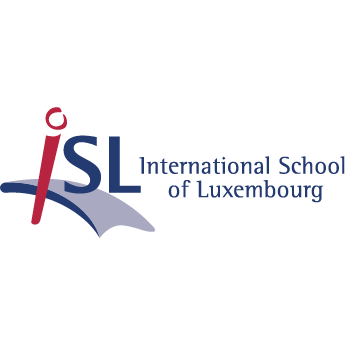
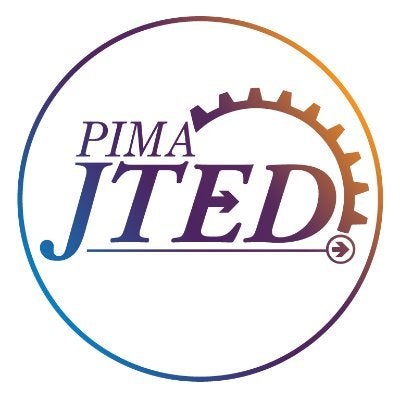
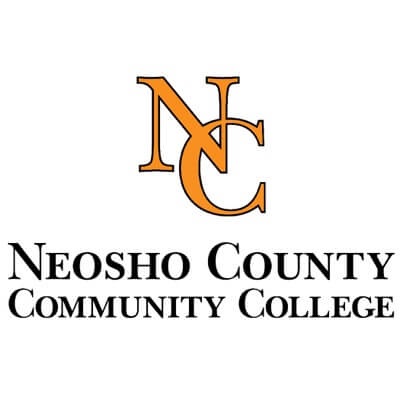
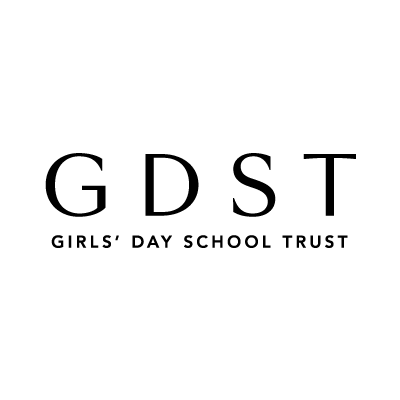
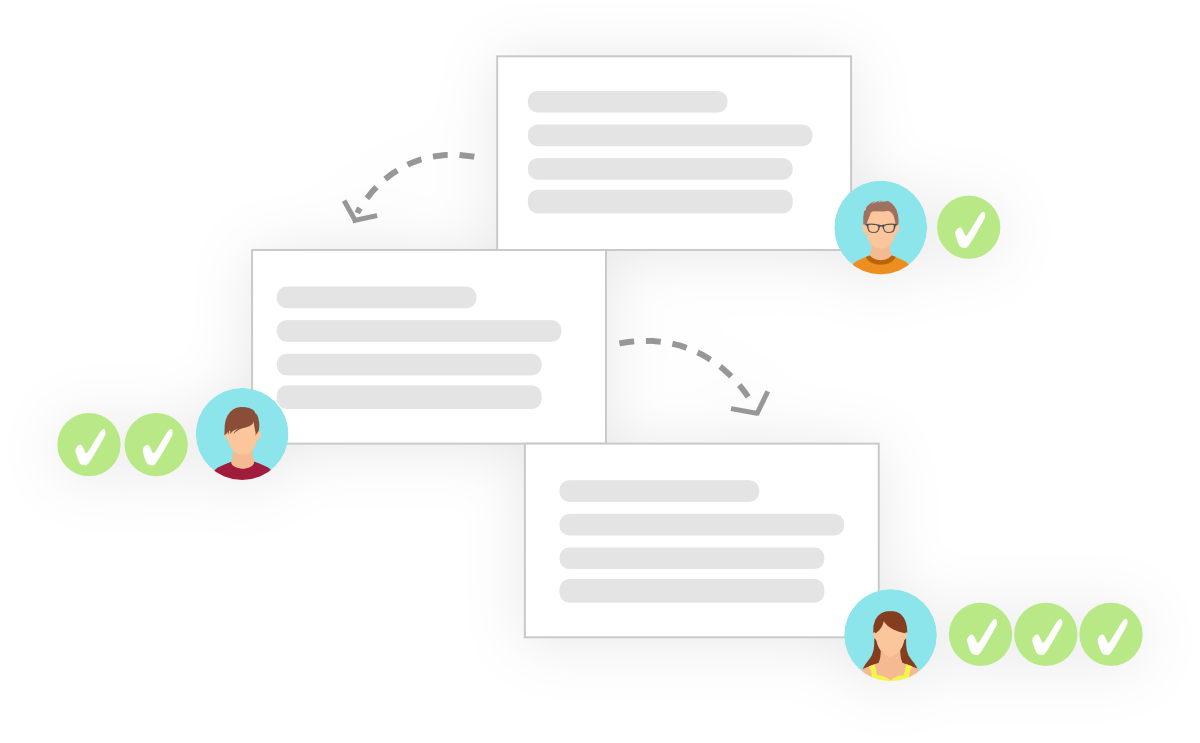
Manage HR processes for manufacturing employees
Handling HR procedures for large scale enterprises such as manufacturing can be time intensive and costly. Minimise these risks by managing all HR processes on your manufacturing intranet, such as vacation and leave requests, recruitment, and appraisal reviews. Store all HR documentation on your digital workplace’s document management system to make sure staff have this vital information at their fingertips.
Create an intranet for everyone – whatever their language
With over 11,000 system messages available to localise, you can create a multi-lingual intranet for your global manufacturing offices. Your content managers can also create multi-lingual Knowledge Base articles, allowing staff to simply toggle to the language that they speak in a single click.

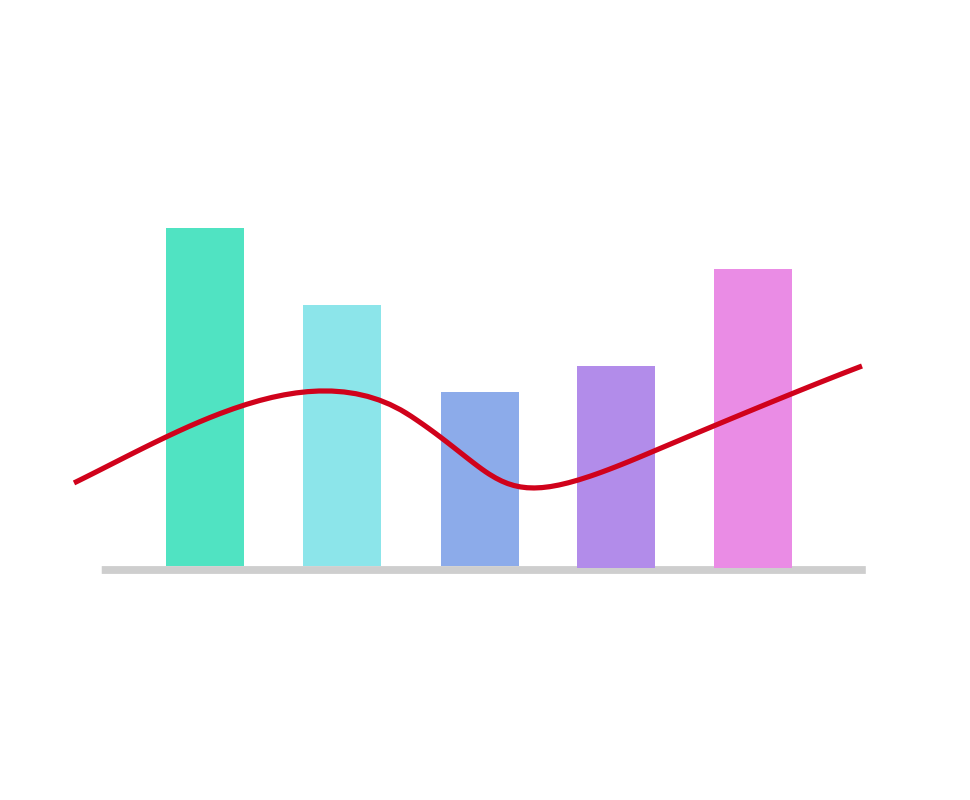
Track financial stats with dashboards
Track your finances and key manufacturing statistics directly on your intranet homepage using our Business Process Management software. Complete with six built-in dashboards that display data at-a-glance, our software allows to you to streamline all your business processes, from product development, to stock control, and budgets, helping to reduce costs and increase efficiency.
Avoid the mass email and staff memos by posting all key events, industry news, and company announcements on your intranet, where content is fresh, real-time, and always accessible. Target news, blogs, and announcements on your intranet homepage so that team members from all locations are up-to-date with the latest developments as soon as they login.
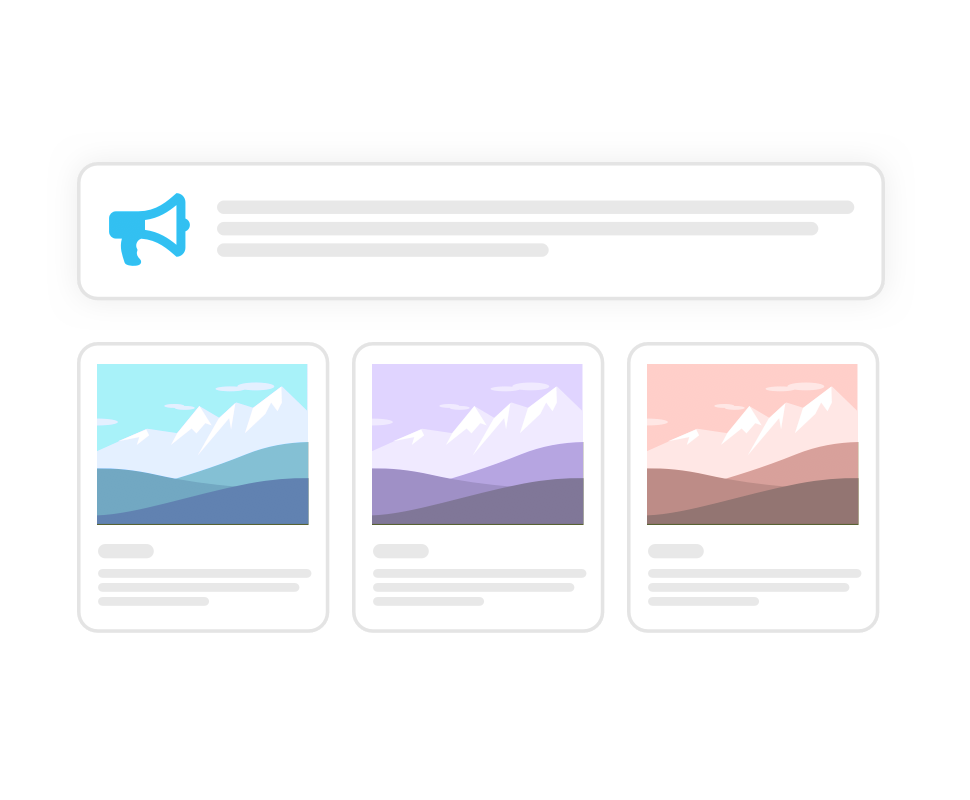
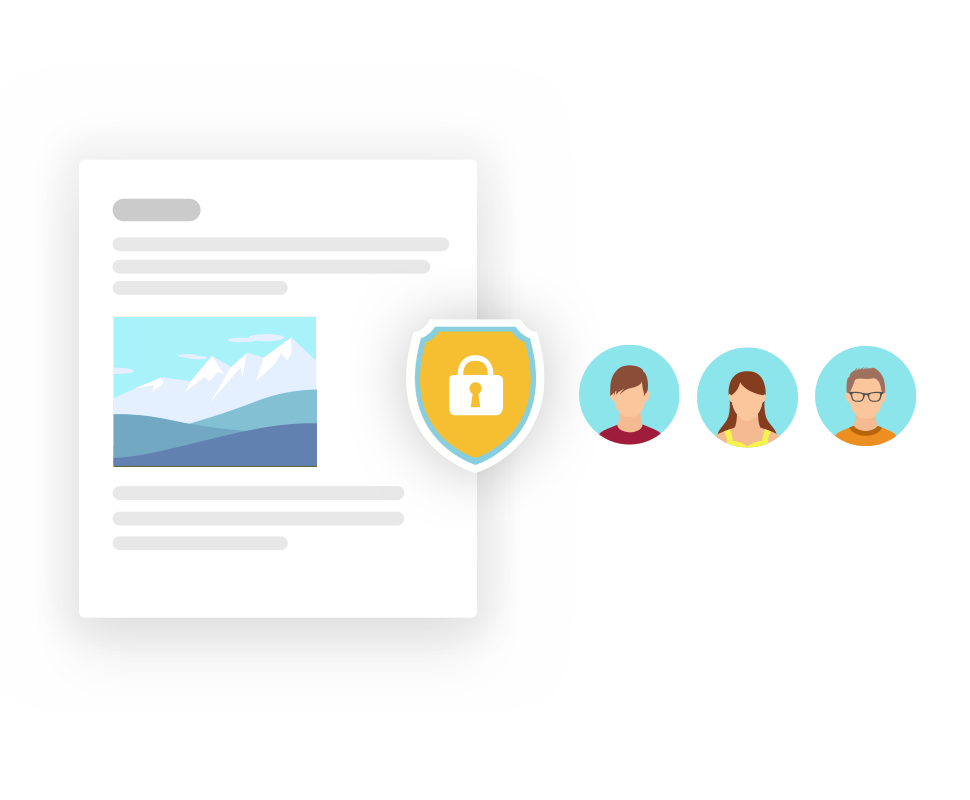
Organise your manufacturing documents
Manufacturing companies will produce reams of documentation, including product descriptions, quality control, and risk assessments. Keep these organised with our Document Management System, which will streamline workflows, manage version control, and improve accuracy. All updates are fully audited too, and you can view previous versions in just a click.
Connect manufacturing staff from across the globe
Have dispersed teams across the globe? Connect them with ease using a digital workplace. Communication tools like corporate social networking, instant messaging, and discussion areas allow staff to communicate and collaborate regardless of their location.
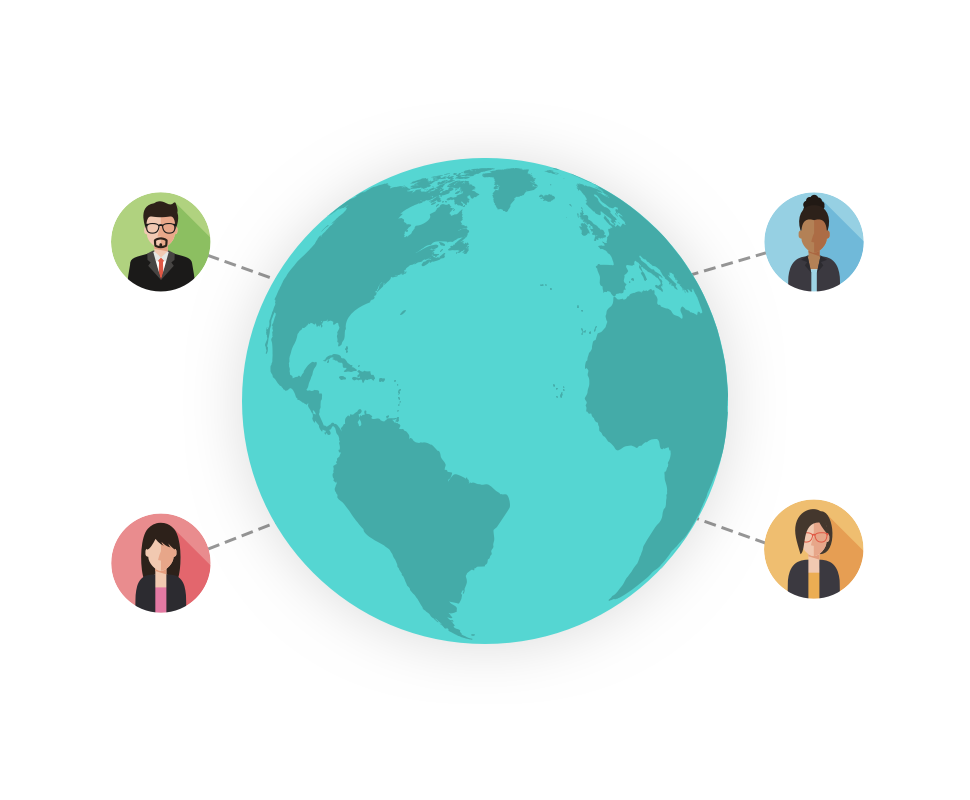