Continuous improvement tools are a vital part of your strategic planning method. If you continuously assess what’s working in your business, what’s not, and how to improve, you’ll see better returns in the longer term.
And knowing when they’re working and when you could be getting more out of them is key to improving business processes.
Workflow automation is essential to the continuous improvement process, because it helps employees to do their jobs better, smarter, and faster. It also enables the company to scale its business by reducing the dependency on manual effort, to achieve the desired results.
Below, we explore what continuous improvement tools are, how you can tell when they’re effective and how to fix common pitfalls.
What are continuous improvement tools?
In a nutshell – any process improvement tools and techniques designed to work incrementally (rather than as a significant one off) are continuous improvement tools.
Many of these originate from the Toyota LEAN production system, which was originally designed to eliminate waste in the company’s vehicle manufacturing process. ‘Continuous improvement’ is a wider net though and incorporates any and all techniques working towards this goal.
Some of the best continuous improvement tools include:
- PDCA cycle: standing for ‘plan, do, check, act’, the PDCA cycle is a systematic approach that encourages an iterative approach to problem solving. It’s one of the most simple improvement tools out there, but super effective at identifying improvement opportunities whilst learning from previous mistakes.
- Gemba walks: getting out of the office and interacting informally with frontline teams in their place of work is known as a Gemba walk. It’s a more informal way of understanding how your business operates and using those insights to drive process improvements.
- Five whys: a simple but effective method of root cause analysis. By asking ‘why’ five times in a row, you force yourself to investigate potential issues in a greater level of detail. You discover both issues and opportunities that a more superficial approach might have otherwise missed.
- Employee surveys: employee feedback is essential for improving current process performance. Using employee survey tools to capture feedback regularly – and then acting on those improvements – improves both key business processes and increases employee engagement.
- Think tanks and focus groups: informal, face-to-face discussion around a particular topic is a powerful improvement tool. Think tanks are a regular group of experts created to solve a particular issue, but you could widen your net with employee focus groups too.
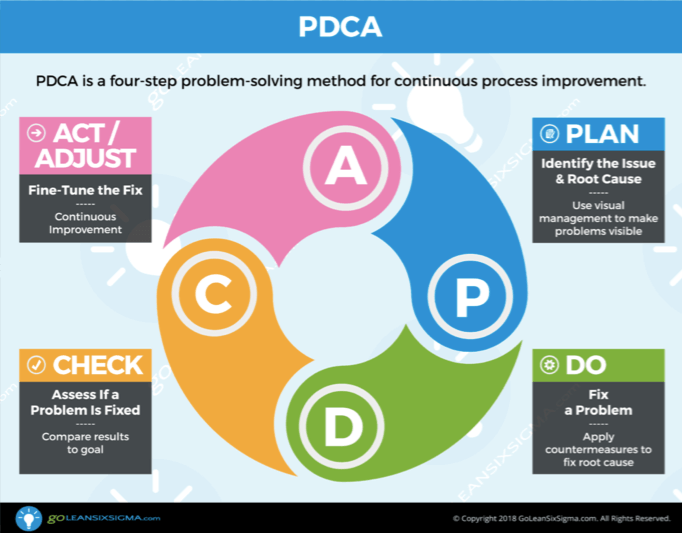
(The PDCA process. Source: goleansixsigma.com)
The above tools could be software-based or software enabled (for example, a survey tool for team feedback) but they don’t have to be. If the tool’s purpose is to improve business processes, it counts as a continuous improvement tool.
How can you tell if continuous improvement is working?
Ultimately, continuous improvement gets results. Over time, you should expect to see efficiency improvements, increased job satisfaction, better compliance management, and greater employee engagement overall. These work together to increase customer satisfaction and increase revenue as a result.
If you’re not seeing these improvements over time – even at a small scale – it might be time to reassess.
Here are four common issues organisations face when trying to improve business operations, and how to overcome them.
1. You’re only using top-down quality improvement processes
The problem
Your managers are dedicated to root cause analysis and employ several process improvement tools to find potential solutions to issues. You might follow one particular system (such as LEAN or Six Sigma), or you might use various techniques from different systems.
What’s missing is one key ingredient: employee feedback. If you don’t use this in your continuous improvement models, you’re cutting out an unparalleled source of operational knowledge from your process improvement practices.
The solution
Use quick pulse surveys to gauge employee opinion on a range of processes. Keep your requests for feedback consistent and focused to allow you to make incremental improvements, rather than running one time-consuming annual feedback form.
You also might want to incorporate more informal ways of gathering employee feedback – so remember Gemba walks, especially if you work in a segregated office or frontline environment. You could also use focus groups to gauge feelings around a particular issue.
2. Your employees don’t stick to daily improvement routines
The problem
You have the best of intentions, and you really want your employees to do well – you’ve painstakingly encouraged everyone to develop daily improvement routines to help achieve this. Whilst people seemed enthusiastic at the start, compliance has dropped off significantly.
The solution
It’s worth investigating if there are any structural reasons for this. Ultimately, your employees want to know whether they will benefit from the effort of a daily improvement routine – does it open up new doors for training or career advancement, for example?
Take a look at your employee reward and recognition processes to understand whether there is more you could be doing.
3. Valuable knowledge about different business areas is siloed
The problem
Your organisation isn’t joined up. You think there might be valuable strategic insights and innovative improvement ideas across many areas of the business, but you have no way of unlocking them due to poor communications processes.
The solution
As organisations adapt to remote and hybrid working practices, investment in knowledge management is expected to increase.
A 2022 survey carried out by KM World suggests that two-thirds of organisations are planning on increasing knowledge management investment over the next 12-18 months.
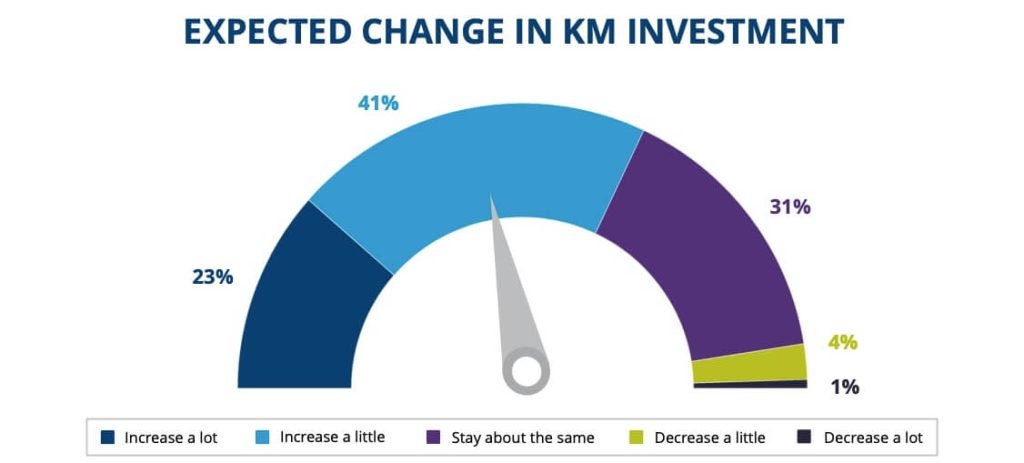
(Expected change in knowledge management investment. Source: kmworld.com)
This is where modern technology shines.
A mobile-friendly intranet brings different strands of the business into a single communications tool. Intranet discussion forums to share knowledge across business areas are a hugely valuable knowledge management tool.
4. No-one uses your continuous improvement software
The problem
You have digital tools in place to facilitate communication and consistent feedback collection, but your workforce doesn’t seem to buy into them at all. Getting people to use these tools – which offer everything from improved productivity to real-time statistical analysis – is an uphill struggle.
The solution
Start by looking at the user experience these tools offer. Are they intuitive, with a clean interface that signposts useful features? Or are they perhaps, more convoluted and confusing than potential workarounds? If it’s the latter, the root cause may be based around ease of use.
Top process improvement tools should always centre usability as a core feature. Look for mobile compatibility to engage remote and frontline workforces, with direct integration into a wide variety of tools for ease of data transfer and analysis.